The Comprehensive Guide to Oil Seal Manufacture
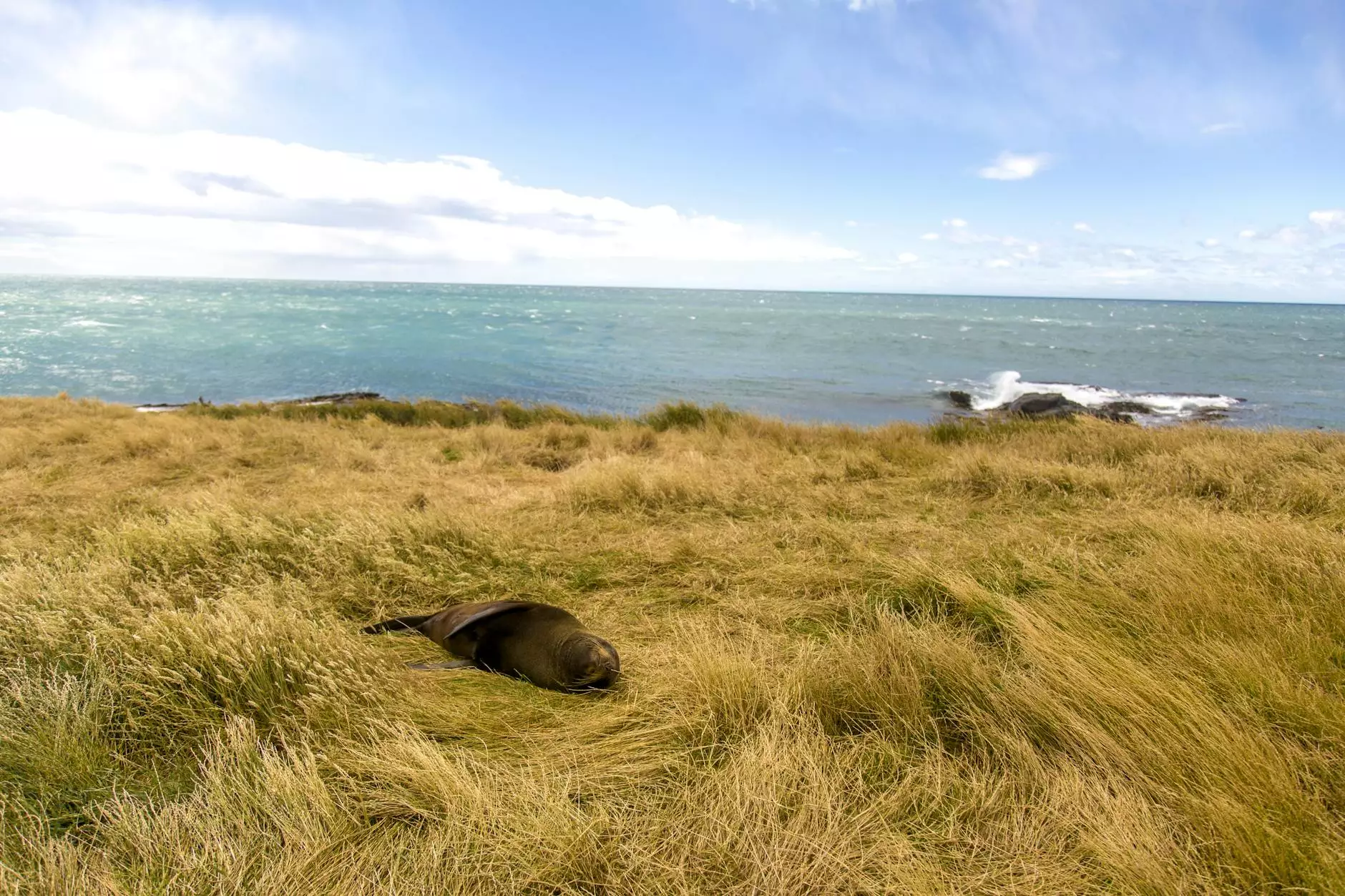
Oil seals are critical components in the world of machinery, especially in diesel engines. Their primary purpose is to prevent oil leakage, ensuring that engines operate efficiently. Understanding the intricacies of oil seal manufacture is essential for quality assurance in diesel engine components. In this article, we delve deep into the significance of oil seals, the manufacturing process, their applications in diesel engines, and why choosing the right supplier is crucial for engine performance.
What are Oil Seals?
Oil seals are mechanical devices designed to retain lubricants in machinery while simultaneously preventing the ingress of contaminants such as dirt and moisture. They are crucial in maintaining lubrication within engine parts, reducing friction, and ensuring optimal performance.
Types of Oil Seals
There are several types of oil seals used in various applications:
- Radial Shaft Seals: These seals are designed to fit around a rotating shaft and are commonly used in diesel engines.
- Mechanical Seals: Commonly used in high-pressure applications, they provide better sealing than traditional oil seals.
- Static Seals: These seals are used where there is no movement between the sealing surfaces, typically in housing assemblies.
The Importance of Oil Seal Manufacturing
The manufacture of oil seals involves precise engineering and high-quality materials to ensure durability and functionality. Poor-quality oil seals can lead to severe engine issues, including:
- Increased Oil Consumption: Ineffective sealing leads to oil leaks, causing engines to consume more oil.
- Engine Contamination: Dirt and moisture can enter the engine, leading to wear and tear.
- Reduced Efficiency: Inefficient sealing reduces engine performance and can lead to costly repairs.
Materials Used in Oil Seal Manufacture
High-quality oil seals are made from a range of materials, each chosen for its properties and application suitability. Common materials include:
- Nitrile Rubber (NBR): Offers excellent resistance to oils and is widely used in oil seal manufacture.
- Fluoroelastomer (FKM): Provides excellent thermal and chemical resistance, making it suitable for high-temperature applications.
- Polyurethane: Known for its durability and resilience, polyurethane is ideal for high-pressure environments.
The Oil Seal Manufacturing Process
The process of oil seal manufacture involves several key steps to ensure the final product meets industry standards:
1. Material Selection
The first step involves selecting the appropriate materials based on the seal's application. Factors like temperature, pressure, and chemical exposure are considered.
2. Design and Engineering
Engineers create detailed designs and specifications for the oil seals, ensuring they meet performance standards and dimensions.
3. Molding Process
Using advanced molding techniques, the selected materials are shaped into these precision components. This process can involve compression molding or injection molding, depending on the design.
4. Quality Control
After the seals are produced, they undergo rigorous testing and quality control checks. Tests include:
- Dimensional checks
- Leak tests
- Material property evaluations
5. Packaging and Delivery
Once approved, the oil seals are packaged securely and delivered to clients, ensuring they arrive in perfect condition.
Applications of Oil Seals in Diesel Engines
Oil seals are used in various engine components to maintain efficiency and reliability. Key applications include:
- Crankshaft Seals: Prevents oil leaks from the crankshaft.
- Camshaft Seals: Ensures that oil remains contained during camshaft rotation.
- Transmission Seals: Protects the transmission fluid from leakage.
Choosing the Right Oil Seal Manufacturer
Selecting the right manufacturer for your oil seals is crucial for ensuring high quality and performance. Here are some tips:
- Experience and Reputation: Choose a manufacturer with a proven track record in oil seal manufacture.
- Quality Assurance: Ensure they have strict quality control measures in place.
- Technical Support: Opt for manufacturers that offer comprehensive technical support and advice.
Client-Diesel.com: Your Partner in Diesel Engine Parts
At client-diesel.com, we understand the importance of high-quality diesel engine components, including oil seals. Our extensive range of diesel engine parts ensures that your engines operate at peak performance. Our commitment to quality and customer satisfaction makes us a leading provider in the industry.
Conclusion
In conclusion, the manufacture of oil seals is a vital aspect of maintaining diesel engine efficiency and reliability. By understanding the manufacturing process, materials, and the significance of choosing the right supplier, you can ensure that your diesel engine operates at optimal performance. Trust client-diesel.com for all your diesel engine parts and repair needs.
For more information, visit us at client-diesel.com and discover the difference that quality parts can make in your diesel engines.